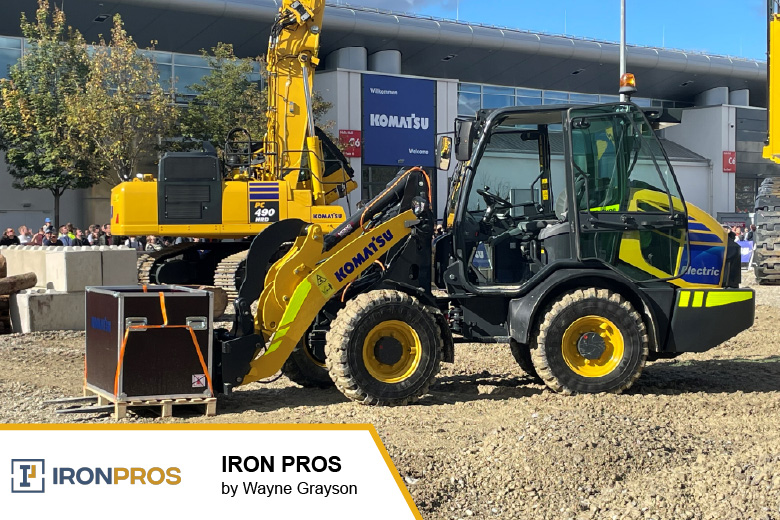
Komatsu unveils All-Electric Loader powered by Moog Construction at bauma 2022
Komatsu recently announced a partnership with hydraulics and electric motor engineering firm Moog to build a fully-electric compact wheel loader. The loader made its public debut at bauma and was demonstrated as part of the Komatsu booth’s daily demo show.
We’ve got all the details in our video overview of this machine and its development.
Just as we’ve done with other fully-electric machines we’ve talked about such as Bobcat’s T7X compact track loader, the point to make with this Komatsu wheel loader is that there are no hydraulics on this machine.
Instead, Moog has replaced the hydraulics with a system that includes electric cylinders for the lift, tilt and steering functions. Komatsu says the fully-electric steering system on this loader has made steering the machine much easier and more efficient than a hydraulically driven loader.
Speed and finesse
Because there is no transmission on this machine, the steering system manages drive as well through an electric actuator and an electric traction motor and includes various software-generated gear ratios to approximate the drive feel operators are used to while making the steering on the machine much more responsive and less tiring. At least for these first electric loaders, Komatsu says they are fine tuning the steering system to have a very similar feel to a hydraulically driven machine. The difference is that through software, Komatsu can offer finer control of the machine with increased speed.
The electric traction motor is a particularly interesting aspect of this system as it allows Komatsu to integrate elements of automation more seamlessly into operation of the machine. For instance, if the machine senses an operator pushing into a pile, the loader would initiate a friction control or an anti-tire-slip function that would allow you to more smoothly dig into the pile and efficiently fill a bucket.
The system also would allow Komatsu to easily implement joystick control on the machine, though joysticks are not as popular on compact loaders as they are on the larger size loaders, redesigning the electrical architecture of the machine does open up that move from pilot controls to E/H controls. The system also includes power electronics, a system control computer, and, of course, a battery and battery management system.
Battery considerations
Komatsu says it is starting its work on electric machines with a compact loader because of the expense of sourcing batteries. Essentially, because batteries are still so expensive, Komatsu feels it only makes business sense right now to implement the technology in smaller machines.
Speaking of the battery inside this machine, it was provided by Moog as part of the company’s retrofit work on this machine.
Moog has become a very popular vendor within the construction equipment market as it has worked with multiple OEMs—including Bobcat and Komatsu—on electrifying their equipment. However, despite this, Moog calls itself power agnostic.
The company’s roots are actually in hydraulics, and the company actually still manufactures hydraulics components in Germany today. However, they have done a lot of pioneering work in industrial fields with electric motors such as work done in aviation to replace hydraulic components with electrically driven ones.
But they’ve also done a lot of work in the fields of robotics and prosthetics and have considerable experience creating electronic motors that provide smooth, predictable motion even at much smaller scales.
The Moog electrification process
Essentially, an OEM approaches Moog with interest in electrifying a machine and then Moog gets to work stripping out all of the internal combustion engine components and hydraulic components and reverse engineering an all-electric solution into that existing machine’s footprint.
For this Komatsu loader, Moog connected its engineering team with Komatsu’s to identify not only the challenges of implementing electric power into this machine, but also to identify what new challenges an electric loader may present to customers in their specific applications.
Once the two engineering teams have identified an average duty cycle of the machine they’re electrifying, Moog sets about redesigning the machine’s architecture, creating an integrated platform of Moog hardware and software.
A fully integrated platform
The software acts as the system’s brain and Moog says it “connects and intelligently coordinates actions across the machine while the all-electric actuators and motors provide the muscle.”
And that integration of hardware and software, that’s where the real power of electrification comes from.
When it comes to electric machines, a lot of people only focus on the runtime of the vehicle. However, the ability to increasing controllability of the vehicle allows operators to accomplish the same tasks in much less time.
When will it ship?
So when can you expect to see this electric Komatsu loader hit the market? There are still several steps for it to pass through on the way to being commercially viable.
Now that there is a working prototype, Moog will get to work creating a version that can be scaled up in production to the first 100 machines or so. Those machines will then be tested in the field among select Komatsu customers.
Then when it comes time for full-scale, long-term production, Moog will continue to provide support by manufacturing key components which Komatsu will integrate into production. Komatsu says this process will likely take up to three years.
In the meantime, Komatsu will also have to decide on a partner for the battery technology at the heart of the loader. Moog provided the battery in the prototype you see in this video, but Komatsu says they will likely explore a deal with Proterra, a U.S. manufacturer of commercial batteries that it already has a relationship with.