An integrated solution allowing a quicker journey to market, streamlined production, and simplified service.
Full electric motion system architecture
Scalable. Modular. Configurable.
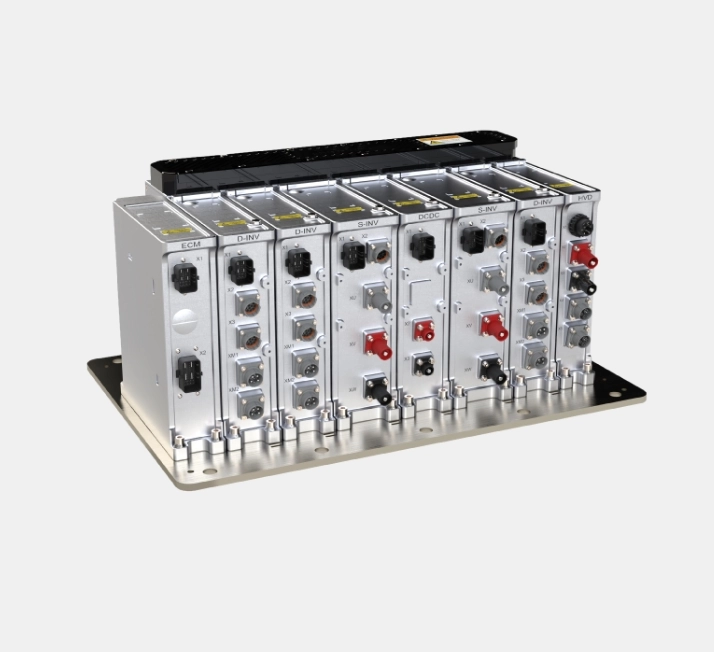
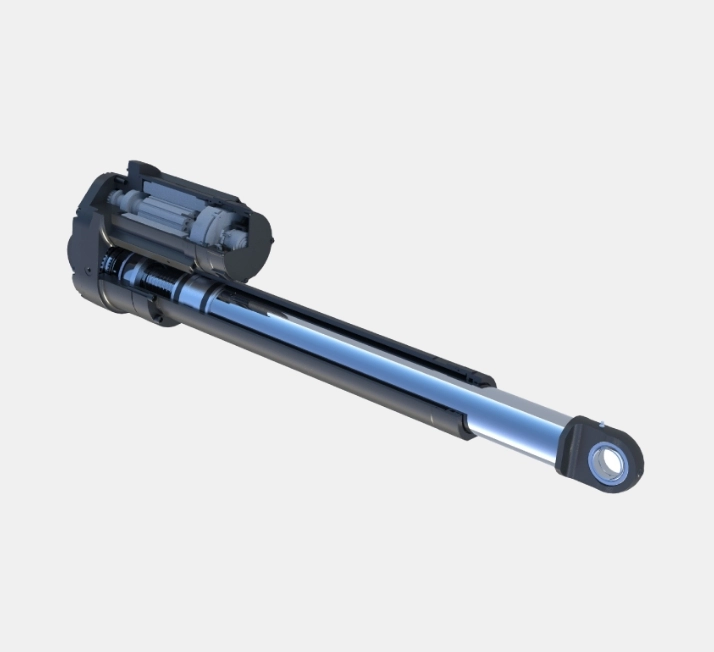
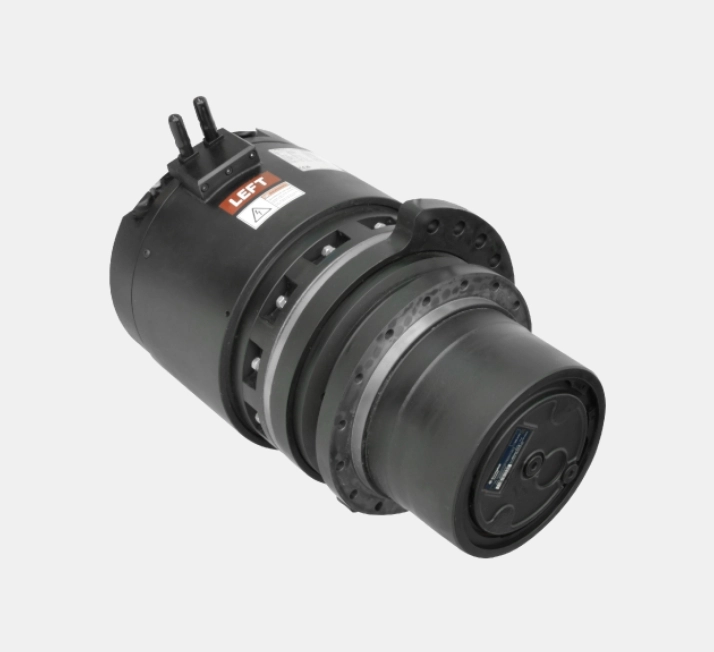
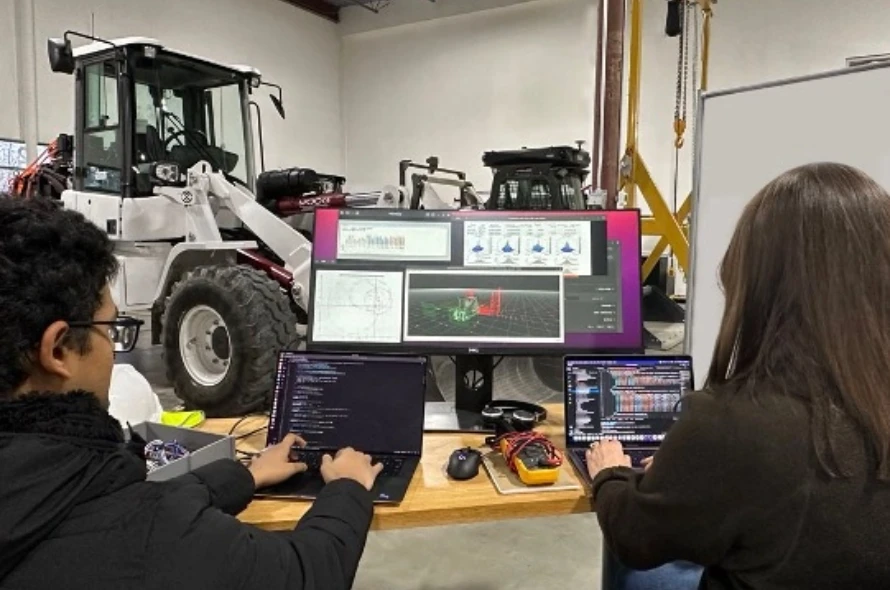
An integrated solution allowing a quicker journey to market, streamlined production, and simplified service.